Alu Fin
Product Range
Fact Sheet
- Location:Maharashtra, India
- Year of Establishment:1978
- Business Type:Manufacturer, Retailer, Business Services
- Turnover:Rs. 5 - 50 Crore
(or USD 1 Million - USD 10 Million) - Main Products:Hard Coat Anodizing, Architectural Anodizing
- Reviews & Rating:
Hard Coat Anodising
Hard anodising was first developed by Russian scientists to produce a metal surface tough enough for space travel. The same technology is now used by ALU-FIN.
- FOB PriceNA
- Min Order QuantityNA
- Payment TermsNA
Other Details
Through a process of electrolysis at sub-zero temperature using a high intensity electric current, 35 to 100 micron thick layer of aluminum oxide (Al2O3) as per requirement is formed molecule by molecule as an integral part of the metal. This process produces a surface harder than steel.
Hard anodising produces harder coatings than the normal 'decorative' process, but the exact shade depends upon coating thickness and anodising conditions (which we can control), as well as alloy, thermal history, degree of hot or cold work, etc, over which we have no control.
ADVANTAGES OF HARD ANODISING
Excellent thermal conductivity.
Good malleability and ductility.
Imparts a surface as hard as some gemstones.
Increase in the surface hardness upto 1000 V.P.N
Excellent lubricating properties especially for continuously moving parts.
Excellent corrosion and abrasion resistance.
Enhancement of working life.
The Hard Anodised surface is non-toxic, non-staining and non-reactive with foods. It is thermal-efficient, heats fast and evenly and is not spoiled by high heat. It is tough and durable, will not tarnish or corrode and will stay looking new for years.
PROPERTIES OF HARD ANODISING
CORROSION RESISTANCE :
The hard anodising process coats the metal with a layer of aluminium oxide, which is chemically inert under neutral, or mild acidic conditions of exposure; it therefore offers a means of protection of the metal surface in a wide range of environments. Because the oxide coating is derived in part from the metal itself, the constituents of the particular alloy have an effect upon the nature of the coating and upon its corrosion resistance (eg Al-Cu alloys) will give a useful measure of protection.
TEMPERATURE RESISTANCE
The anodizing process applies to the metal surface a coating of aluminium oxide. The nature of the process is such that adhesion of the oxide to the substrate can be taken for granted, unlike ceramic and other coatings which are dependant upon cleanliness and other factors. The melting point of aluminium oxide is over 2000C, which is far above that of the metal itself, and it is largely unaffected by temperatures within the useful range of the metal.
ELECTRICAL INSULATION
The coating produced by the anodising process is composed of aluminium oxide, a material having exceptional dielectric strength. The coating has excellent adhesion to the substrate, high resistance to mechanical damage and extremes of temperature making anodising aluminium the preferred choice of a number of electrical applications.
WEAR RESISTANCE - HARDNESS TESTING
The coating produced by the hard anodising process is chemically akin to many gemstones and shares their property of extreme hardness and resistance to abrasion. The hardness of anodised coatings is specified in British Standards using the Vickers Micro Hardness Test in which the hardness is measured on a section through the film giving micro hardness values of 250 to 100 VPN; depending on the aluminium alloy, the process and the sealing.
The matrix of aluminium oxide itself has a micro hardness of around 1,100 Vickers. The indentation method of the Vickers Test really indicates the crushability of the brittle and porous anodic film whereas the property often expected by customers is abrasion resistance.
Images
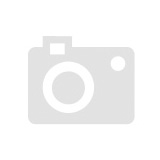